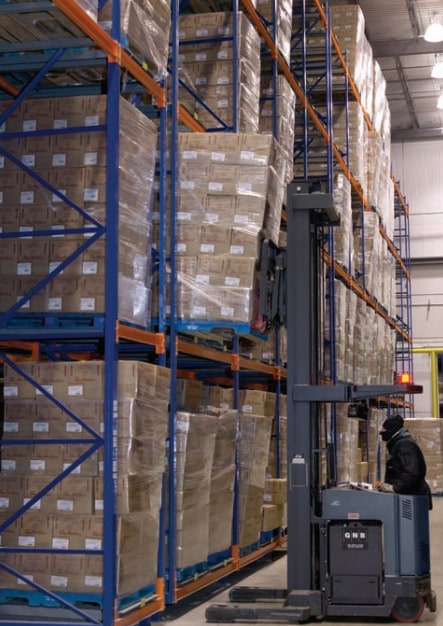
Push back racks offer the same storage density as drive-in racks but greater selectivity. All loads are stored and retrieved from the aisle. Loads in each lane rest on a cart on a rail that slopes slightly toward the front. When a new load is deposited into a lane, it ‘pushes back’ the one already at the face and all of those behind it. Then, when that load is picked, the contents of the lane all move forward again, hence the term “Push Back Rack”.
The objective of push back rack is to reduce honeycombing or empty pick faces. The ideal application for push back racks is where all loads in a lane are identical and first-in/first-out stock rotation is not crucial.
HOW DO PUSHBACK RACKS WORK?
A pushback system contains a pair of inclined rails and a series of nesting carts which ride on these rails. As an example, a 4 deep lane will have 3 nested carts. The first pallet is loaded on the top cart by a forklift. When the operator comes in with the second pallet, he pushes the first pallet back and rests the second pallet on the middle cart. Similarly, the 3rd pallet pushes back the first 2 and rests on the bottom cart. The operator loads the last pallet by pushing back the first 3 and placing the load on the pair of rails.
When unloading, the sequence is reversed. Because the rails are inclined toward the aisle, when the operator picks up the pallet resting on the rails and backs out, the 3 remaining pallets will follow to the front of the lane. He can then remove each pallet in succession, until the lane is empty.
WHO USES PUSHBACK?
Our products are installed in a wide variety of industry types including food distribution, manufacturing, 3rd party logistic facilities, automotive and pharmaceuticals. Almost any warehouse that is looking to increase their storage capacity is a potential candidate for pushback rack. Pushback systems are fully operational in freezers or coolers and no special forklifts are required.
WHY USE PUSHBACK VERSUS DRIVE-IN RACK?
Because the pallets come to the aisle, pushback is much faster to load and unload than any comparable drive-in rack. Additionally, stock rotation and occupancy are greatly improved because each level can store a different product in pushback. Finally, rack damage is significantly reduced because the operator does not have to drive into the rack to remove pallets.
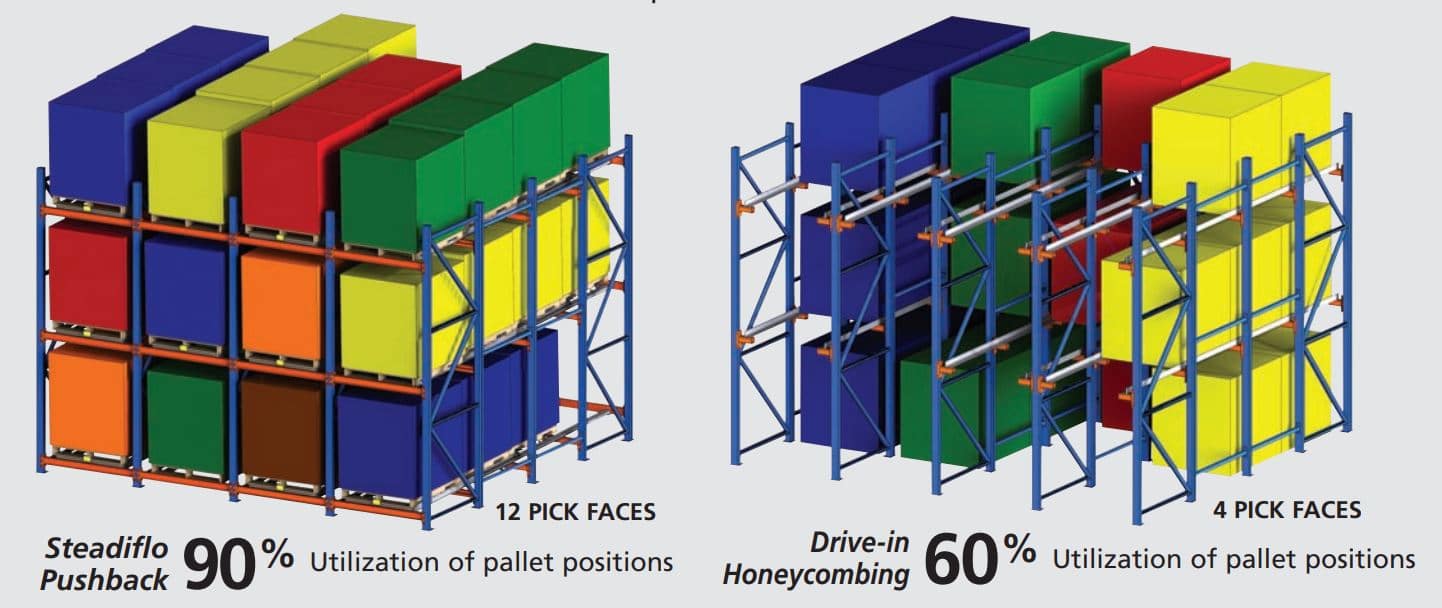
STEADIFLO PUSHBACK FEATURES AND BENEFITS
- LOW PROFILE
- LINKED CARTS
- MULTI PURPOSE PLATE / SAFETY STOP
- LIFT-OUT PROTECTORS
- FLANGED STEEL WHEELS
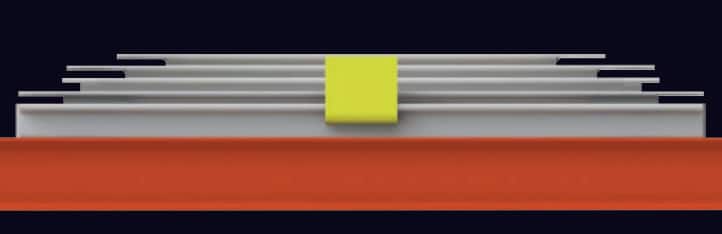
LOW PROFILE
Steadiflo has a lower profile than other cart type systems. This allows for extra lift clearance and may even mean the difference of an extra level.
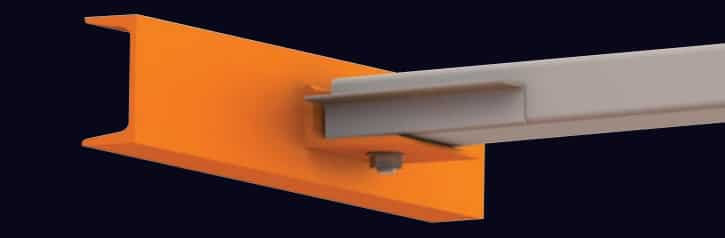
LINKED CARTS
Carts are linked when extended, eliminating the possibility of single pallet hang-ups. Without this feature, it would be possible for a pallet to become temporarily lodged at the back of a lane, release, and travel in an uncontrolled manner to the load end. The result, potential for damage to product and personal injury.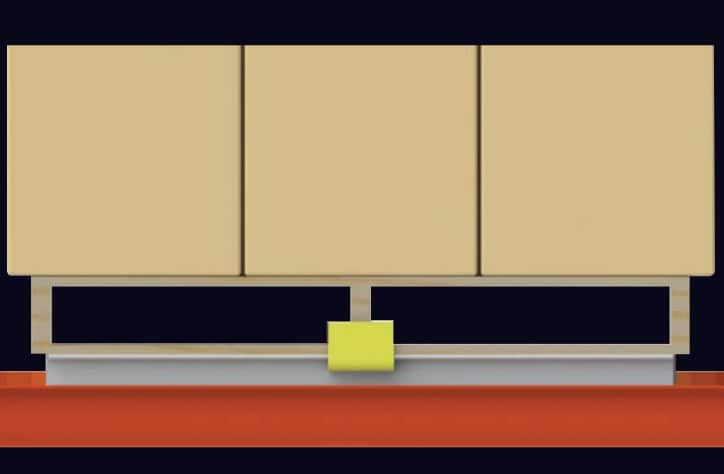
MULTI PURPOSE PLATE / SAFETY STOP
- Height Gauge – When loading a pallet, the operator knows that if the load is high enough to clear the safety stop, then the pallet will not prematurely move the awaiting cart.
- Strip-Off Stop – If, after placing a pallet, the operator has his forks in an improper tilt position, the safety stop will catch the bottom of the pallet and “strip” it off his forks.
- End Stop – The safety stop, which is situated on the lowest cart and protrudes 3/4” above the highest cart, prevents pallets from shifting beyond the front load beam.
- Push Plate – Pushing on the plate with the last pallet being inserted into the lane ensures proper placement on the rails.
- Lane Full Indicator – The operator can tell if a lane is full by the absence of the safety stop. If it is not showing at the front, the last cart has been loaded and there is a pallet on the rails – a full lane.

LIFT-OUT PROTECTORS
Each cart is equipped with lift-out protectors, which prevent accidental dislodgement of a cart by the forklift operator.
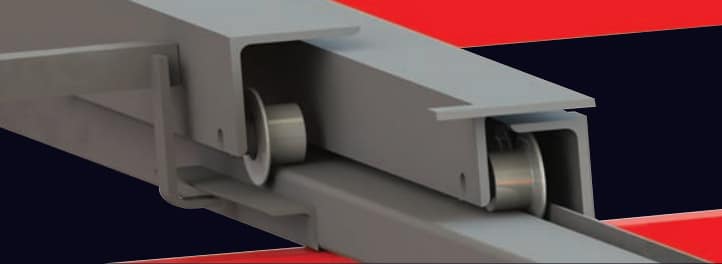
FLANGED STEEL WHEELS
Wheels are manufactured using solid steel and are equipped with heavy-duty bearings. Sturdy 5/8” shafts are welded to the carts and are oversized to withstand shock loads of up to 1,400 lbs. per wheel.
PUSHBACK LAYOUT GALLERY
READY TO START YOUR PROJECT?
Contact us today to discuss your needs.