How to Increase Warehouse Storage Capacity
Ways to Increase Warehouse Storage Capacity |
---|
1. Implement a Storage System |
2. Increase Density of Existing Storage System |
3. Install an Industrial Mezzanine Floor |
4. Invest in Automated Storage |
5. Re-organize your Facility Layout |
6. Building Modification (i.e. building expansion) |
7. Relocate |
We will explain these options in more detail, but first let’s discuss the advantages of increasing your warehouse storage capacity:
- Increase product scale and scope
- Decrease lead times for your end-users
- Improve customer service
Ultimately, increasing your warehouse storage capacity is an investment in your business that will yield higher profits in the long run. Furthermore, taking steps to increase warehouse storage capacity will ensure that you are staying competitive in your industry. Lead times, product availability, and customer service are traits that are becoming more and more important to consumers and purchasers alike. By increasing warehouse storage capacity, you will be able to offer shorter lead times, and store more of your existing products, as well as store an increased variety of products.
It is important to note, that to increase warehouse storage capacity while remaining competitive, it must be done in an efficient manner to ensure that you maintain operational efficacy. Increasing warehouse storage capacity may feel like a daunting task, but there are multiple options for you, so that you can make the right choice to meet your goals and budget.
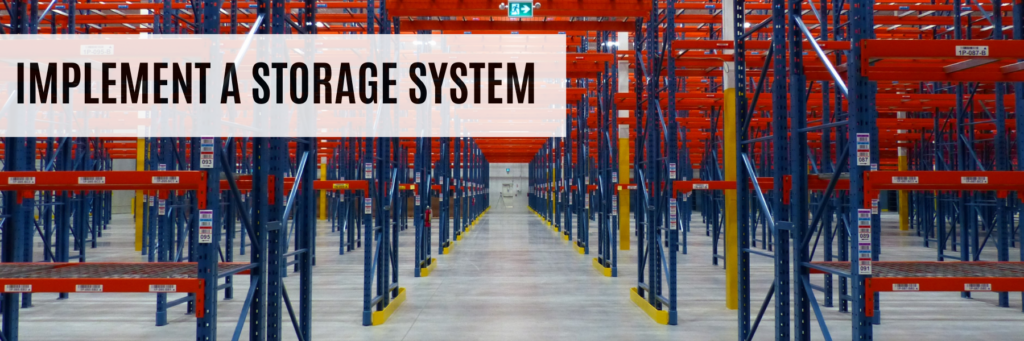
Does all your available space in your warehouse currently have a storage system installed? If not, this should be your first order of business. Many businesses starting out only get a storage system for a portion of their warehouse space. If there are areas in your warehouse that do not have a strategic and well-planned warehouse storage system erected, then filling these gaps will greatly increase warehouse storage capacity.
Â
 A selective pallet racking storage system can be installed relatively quickly, and provides storage that is easily accessible by a forklift. However, selective pallet racking is not the most dense storage system available.Â
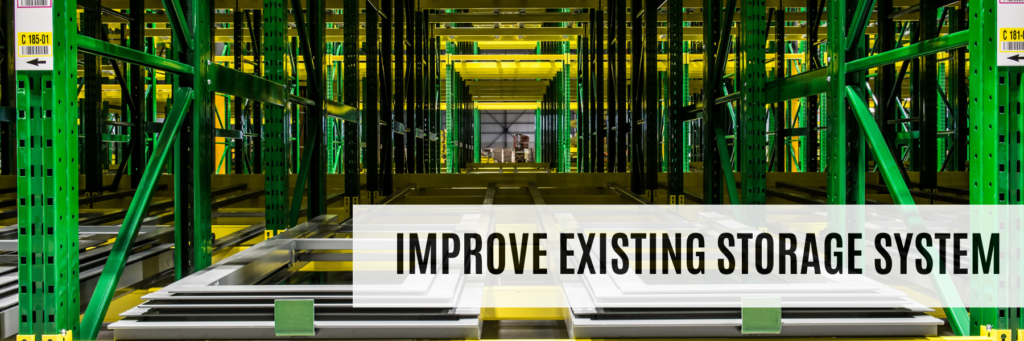
If you have an outdated storage system, perhaps it’s time for an upgrade to increase your storage density. For example, upgrading from selective pallet racking to drive-in racking, push-back racking, or pallet flow systems will greatly improve the capacity of your warehouse.
Â
 Additionally, you can use this as an opportunity to inspect your current system for any damage or areas that need to be improved due to safety standards. The experts at Concept Storage Solutions can provide an inspection of your warehouse storage system and the racking storage solutions that are currently in place, and provide you with guidance and advice to improve them.Â
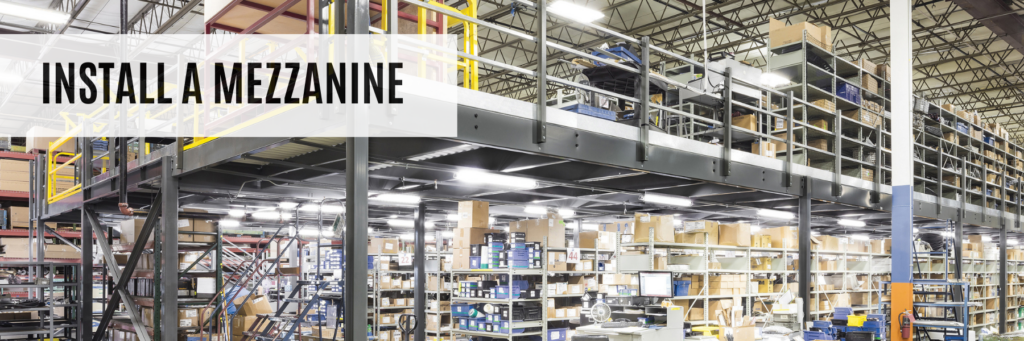
Implementing an industrial mezzanine floor to your warehouse is a great way to utilize available vertical space that you already have, but typically goes unused due to inaccessibility. Warehouse mezzanines and storage platforms are a preferred alternative to a building addition or relocation because a mezzanine installation is much quicker, cost effective and puts less of a burden on your daily operations than the former two options.
Mezzanines are customizable and therefore can be designed to meet your business’ specific needs. Unlike a building addition which is permanent, warehouse mezzanines are modular, and can therefore be moved if needed.Â
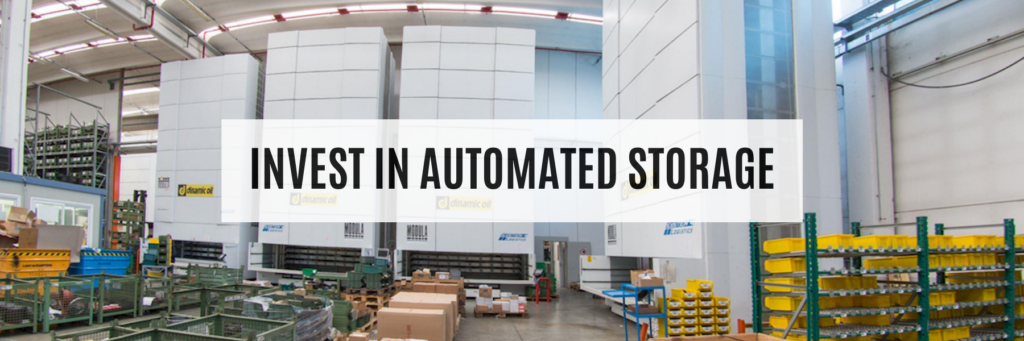
Automated storage and retrieval systems are revolutionizing how organizations are handling their materials. These state of the art solutions allow for huge cost savings in labour, greater accuracy of order picking, enhanced safety and security, and an impressive reduction in space requirements.
Vertical Lift modules are able to use vertical space in your warehouse that may have gone un-used, therefore increasing your storage capacity. Furthermore, Vertical Lift modules can convert 9,050 sqft of traditional storage, into only 150 sqft; all while increasing product accessibility.
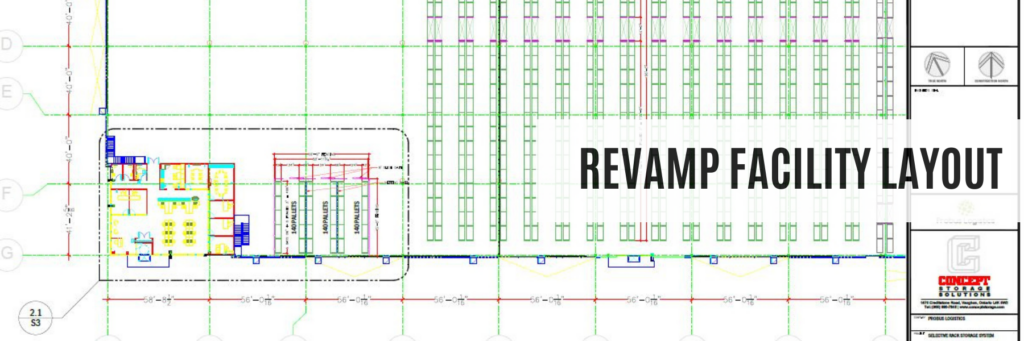
You might not be making the most of your available warehouse storage space due to an inefficient facility layout. By relocating some of the major components of your warehouse storage system, or completely revamping the layout, you might find that you can make much better use of your space.
Our team at Concept Storage Solutions has decades of experience in facility layout design and services such as: final detailed plans and elevations required to establish storage yields for customer inventory control, in-house prototype testing at our facility for pallet flow systems, certified engineering drawings for building permits, fabrication drawings required for production.
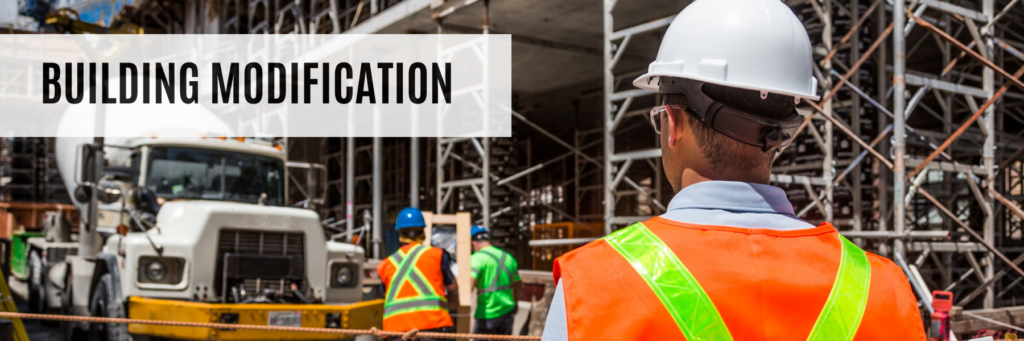
Although building modifications are seldom an
option for businesses in leased facilities, it is sometimes one of the last
resorts to increase warehouse storage capacity.
The advantage of a building modification is that it will have less of a
disruption to your daily operations than re-locating. However, the disadvantage
is that building modifications (like an expansion) take time, and often are met
with lengthy delays due to building permits, labour shortages etc. Furthermore,
building modifications are expensive.
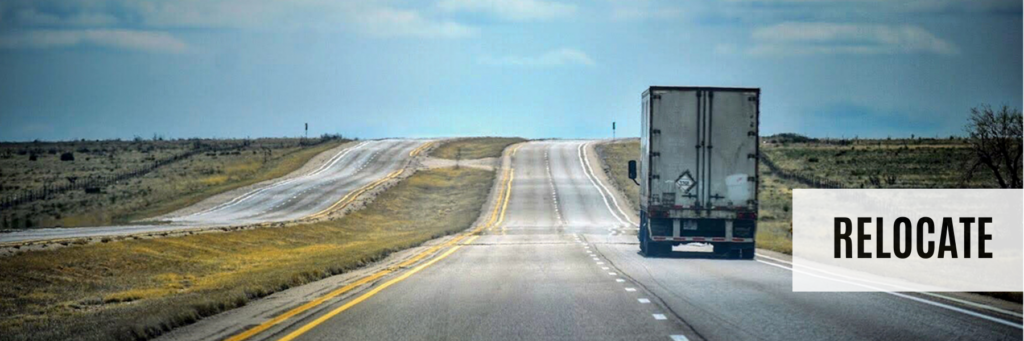
If the storage capacity within your warehouse just isn’t cutting it, even with the help of a warehouse storage expert or the suggestions above, it may be time to relocate. The needs of a company changes as time goes on, meaning you might grow out of your current warehouse.
Relocating warehouses can give you the opportunity to invest in a site that has room for future growth, improve your current warehouse storage system, and make any other changes necessary as your company evolves.
Â
For help relocating your warehouse storage system, contact the experts at Concept Storage Solutions today. We offer a variety of products, services, and various warehouse storage solutions